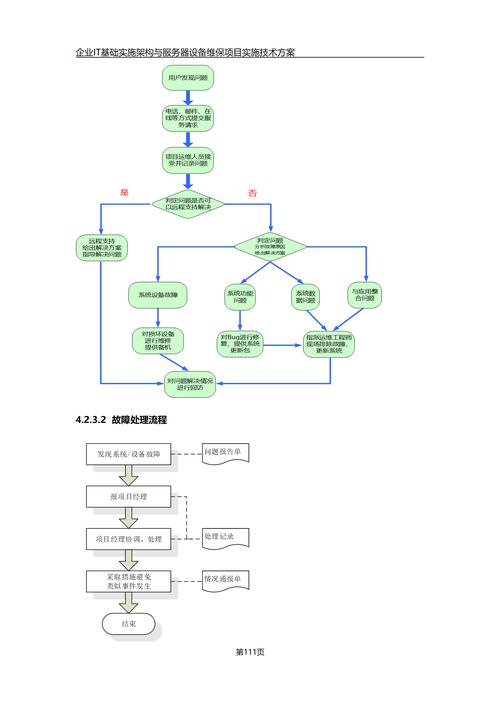
故障现象的精确描述与记录
完整的故障排除始于对异常现象的准确捕捉。操作人员需要记录故障发生时的环境参数(如温度/湿度)、设备运行状态指示灯、错误代码显示等关键信息。对于间歇性故障,要特别注明发生频率和持续时间。工业设备还需记录故障前后三分钟的设备运行参数曲线。建议建立标准化的故障报告模板,包含现象描述区、影响评估区和初步诊断区三个模块。现代智能设备可通过SCADA系统自动生成包含时间戳的故障快照,大幅提高信息采集的完整性。
诊断工具的选择与应用技巧
根据故障类型选择适当的诊断工具能事半功倍。硬件层面需准备万用表、示波器、热成像仪等基础工具,软件诊断则需配置日志分析系统、网络抓包工具和性能监控平台。特别要注意诊断工具的精度等级需高于被测设备指标,如测量变频器输出时需选用带宽100MHz以上的隔离示波器。对于复杂系统故障,建议采用分层诊断法:先通过设备自带的LED指示灯或蜂鸣器代码确定故障大类,再用专业工具进行模块级诊断,定位到具体元器件。网络故障要遵循OSI七层模型从物理层开始逐层排查。
典型故障模式分类与特征识别
机械类故障多表现为异常振动、噪声或温升,其发展往往呈现浴盆曲线特征。电气故障常见短路、断路和接地异常,可通过绝缘电阻测试和回路阻抗测量识别。软件故障主要分为内存泄漏、线程死锁和资源竞争三类,在日志中会留下特定模式的错误记录。网络故障需区分是物理连接问题(如光纤断裂)、协议配置错误还是带宽拥塞。工业控制系统还要特别注意信号干扰导致的偶发性故障,这类问题在接地系统不良时尤为突出。
分步解决方案的制定与验证
制定解决方案时要遵循"最小影响"原则,优先采用参数调整等软性处理方式。对于必须更换硬件的情况,要确保备件型号完全匹配并做好静电防护。复杂系统的修复需编制详细的回退方案,建议采用变更管理中的5W1H方法(What/Why/Who/When/Where/How)记录每个操作步骤。解决方案实施后必须进行72小时以上的连续运行测试,期间要特别关注设备启动特性、稳态运行参数和负载突变时的响应表现。网络系统修复后还需进行吞吐量测试和延迟测量。
故障根本原因分析与预防措施
完整的故障排除不应止步于表面修复,而要通过5Why分析法追溯根本原因。某PLC频繁死机的直接原因是内存溢出,深层原因可能是扫描周期设置不当导致任务堆积。预防措施应包括技术和管理两个维度:技术方面要建立设备健康度评估体系,设置关键参数的预警阈值;管理方面需完善点检制度,制定预防性维护计划。对于共性问题,应更新FMEA(故障模式与影响分析)数据库,并将典型案例纳入员工培训教材。
系统化的故障排除流程包含现象捕捉、工具诊断、模式识别、方案实施和预防改进五个关键环节。掌握标准化的排查方法能缩短设备停机时间,而深入的根本原因分析则可以有效降低故障复发率。建议企业建立包含故障知识库的数字化运维平台,将个人经验转化为组织能力。常见问题解答
Q1:如何区分硬件故障和软件故障?
A1:硬件故障通常伴随物理状态异常(如发热、烧焦味),且重启后问题依旧;软件故障往往通过重启可暂时恢复,且在日志中有明确错误记录。
Q2:偶发性故障该如何排查?
A2:对偶发故障需延长监测时间,使用带历史记录功能的检测设备,必要时可故意制造负载波动等边界条件来复现故障。
Q3:没有错误代码时如何开始诊断?
A3:采用排除法,从电源系统开始检查,依次验证通信链路、传感器信号和执行机构,同时对比正常设备的标准参数。
Q4:多设备系统故障如何定位责任点?
A4:通过分段隔离法,逐个断开子系统连接,观察故障现象变化,同时分析各子系统间的交互时序是否匹配。
Q5:预防性维护真的能减少故障吗?
A5:统计数据表明,规范的预防性维护可使意外故障降低60%以上,特别对机械磨损件和电解电容等寿命明确的元器件效果显著。